Il processo di zincatura garantisce una protezione con ben aderente che risulta durevole nel tempo, aumentando così la vita dell'acciaio. Per un'operazione efficiente, è importante che il forno di zincatura applichi il calore in modo costante e uniforme su tutta la larghezza del nastro di acciaio.
Il processo di zincatura in breve
Il processo di zincatura prevede l'applicazione di un rivestimento di zinco protettivo sull'acciaio. Ciò si ottiene immergendo l'acciaio nello zinco fuso e mantenendolo a una temperatura di circa 460°C in modo che si leghi metallurgicamente alla superficie dell'acciaio e formi una lega di ferro zinco. Quando l'acciaio ritorna a temperature ambiente, si forma uno strato protettivo che aiuta a prevenire corrosione e ruggine.
"Se la temperatura non è uniforme, anche lo spessore del rivestimento e le proprietà dell'acciaio saranno diversi", afferma Susanne Selin, Senior R&D Project Manager di Kanthal. "Si vuole davvero essere in grado di controllare la temperatura nelle diverse zone del forno ed essere anche in grado di adattarla rapidamente quando cambi il prodotto in acciaio durante la lavorazione."
Vantaggi del riscaldo elettrico rispetto a quello a gas
Susanne Selin, Senior R&D Project Manager, Kanthal.La soluzione di riscaldo più comune utilizzata nei forni di zincatura sono i riscaldatori a gas. Tuttavia, un'alternativa sempre più praticabile è quella elettrica. Il più grande vantaggio del riscaldo elettrico è il suo migliore controllo della temperatura, il che consente agli operatori di raggiungere valori precisi nelle diverse zone del forno. Inoltre, l'efficienza termica è decisamente maggiore poiché non viene disperso calore attraverso i fumi di scarico.
"Sostituendo i riscaldatori a gas con quelli elettrici, è possibile eliminare tutto l'inquinamento e i fumi, oltre a ridurre significativamente il livello di rumorosità", afferma Selin. "Il riscaldo elettrico migliora inoltre la sicurezza sul lavoro e riduce la necessità di molti lavori di manutenzione, poiché elimina tutti i potenziali problemi di sicurezza legati all'uso del gas."
Una soluzione senza problemi
Sulla base della sua pluriennale esperienza nel riscaldo elettrico industriale, la soluzione ottimale di Kanthal per i forni di zincatura sono i suoi elementi riscaldanti Tubothal® abbinati a tubi radianti nelle leghe ferro-cromo-alluminio (FeCrAl) Kanthal® APM o Kanthal®APMT.
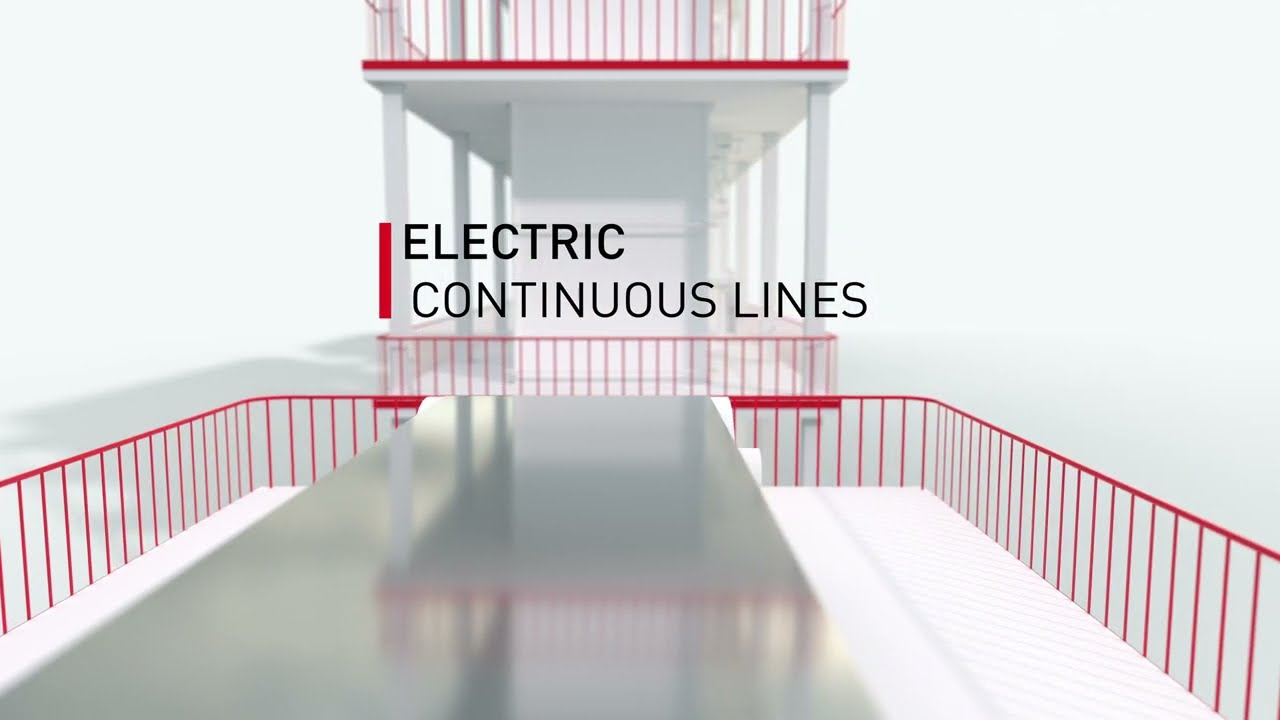
Se si tiene conto dei risparmi per la manutenzione e del minor consumo energetico, questa diventa una soluzione molto conveniente.
"Entrambe queste leghe si comportano molto bene in tutti i tipi di atmosfere di lavoro, sia in termini di resistenza all'ossidazione sia alla corrosione", afferma Selin. "Sono necessarie molte meno operazioni di pulizia e manutenzione rispetto agli elementi riscaldanti tradizionali. Se si tiene conto dei risparmi per la manutenzione e del minor consumo energetico, questa diventa una soluzione molto conveniente."
Sei vantaggi del riscaldo elettrico nei forni di zincatura
- Miglioramento dell'efficienza termica: Rispetto ai riscaldatori a gas, una parte molto maggiore del calore generato da un riscaldatore elettrico viene utilizzata nel forno anziché dispersa con i fumi di scarico.
- Controllo preciso della temperatura: Rispetto al gas, un riscaldatore elettrico può essere controllato per fornire temperature precise.
- Eccellente uniformità della temperatura: il riscaldo elettrico fornisce una temperatura costante e uniforme su tutto il nastro in acciaio.
- Ambiente di lavoro più pulito, più sicuro e più silenzioso: i riscaldatori elettrici non emettono fumi di scarico nocivi in fabbrica e i livelli di rumore sono molto più bassi.
- Zero emissioni di CO2: Se il riscaldatore elettrico è alimentato da energia rinnovabile, allora il processo non produce emissioni.
- Manutenzione minima: Con una ridotta ossidazione, diventeranno necessarie una minore manutenzione e una minore pulizia legata ai sottoprodotti della combustione o alla formazione di scaglia dagli elementi.
Scopri di più
L'elettrificazione resa semplice