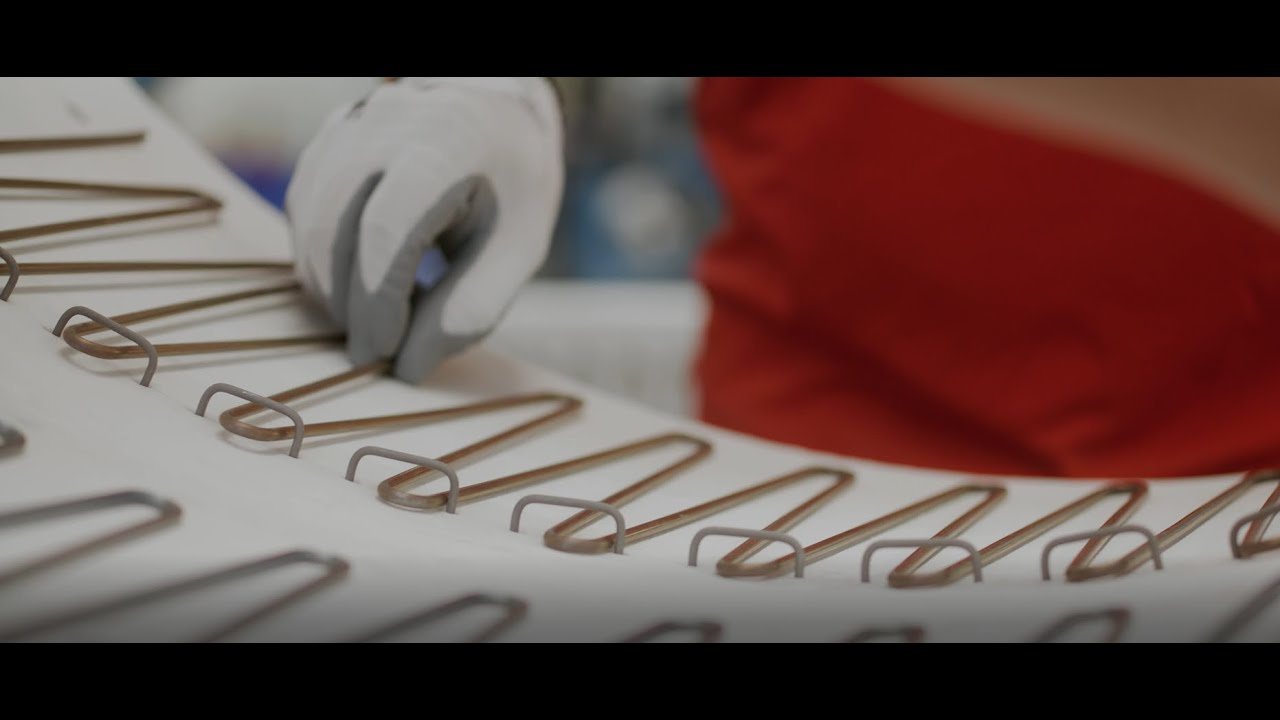
Markus Mann, Manager Technology Innovation, Kanthal“When we started making Fibrothal® back in 1978, I don’t think anyone could have imagined it would become as big as it is today,” says Markus Mann, Manager Technology Innovation at Kanthal’s plant in Walldorf, Germany.
When Kanthal first started producing Fibrothal®, it was seeking to solve the considerable challenge of combining ceramic fibers, such as blankets or folding blocks, with electric heating elements in an electrically heated furnace. These days, the Fibrothal® range encompasses a family of products consisting of vacuum-formed ceramic fiber components, with or without electric heating elements.
Extensive testing
“At Kanthal, we believe customers should never have to settle for ‘good enough,’ which is why all Fibrothal® solutions are tested extensively during development and continuously improved in partnership with furnace builders, to make sure they are easy to use and install,” says Mann.
Fibrothal® combines insulation and heating elements in one innovative system that delivers both excellent insulation and a custom-made heating solution. It is quick to install, while its modular setup makes it easy to tailor to specific customer needs.
“Depending on the individual application, we can design and optimize it to save energy,” says Mann. “There’s nothing else on the market like Fibrothal®!”
Fast installation
Traditionally, making a kiln was a very time-intensive process, often involving weeks of brick-lining work. With Fibrothal®, this implementation can be completed in as little as one to two days, due to the modular nature of the system.
However, as Mann is quick to point out, no two processes are ever exactly the same.
If you have the right heating elements and design made from the right alloys, what you will get in exchange is high performance and long service life, high uptime and excellent productivity
“There’s a reason why we are a market leader with Fibrothal®: the experience we have built over the decades allows us to squeeze the most out of the technology,” he explains. “Having produced and developed Fibrothal® for decades, we’re very confident in our ability to deliver exactly what the customer process requires. And what it ultimately comes down to, is this: if you have the right heating elements and design made from the right alloys, what you will get in exchange is high performance and long service life, high uptime and excellent productivity.”
Joint development with customers
Ines Nickel, process engineer, KanthalWhen it comes to developing Fibrothal®, nothing is left to chance. Mann explains that Kanthal has its own laboratory where it tests its products and processes to their limits. It then carries out optimizations to ensure that Fibrothal® is ready to meet the growing demands of the future.
“Our development process takes place jointly together with our customers,” he says. “We take their input seriously and funnel their feedback into our development process to make sure our products and solutions meet their needs.”
So, where is Fibrothal® used?
“If an industry works with high temperatures, Kanthal brings the heat,” says Ines Nickel, process engineer at Kanthal. “No heat is too hot for Kanthal!”
Future-proof technology
“Fibrothal® has very low thermal conductivity, which means it saves energy,” she says. “And saving energy is the future.”
Another crucial factor that cements the product’s status as a future-proof technology is, of course, that it provides fossil-free electric heat.
Nickel explains that Fibrothal® can essentially be used in any application that requires high temperatures for industrial processes. This includes, but is not limited to, heat treatment for the aluminum, semiconductor and lithium-ion industries.
Fibrothal® for acid roasting
Fibrothal® heating moduleFibrothal® has proven itself as an effective heating solution for the lithium-ion industry and, more specifically, the acid roasting process that takes place during lithium refining.
“This is a process that happens at moderate temperatures,” Mann explains. “What that means is that you can achieve very high energy density when using electric heat.”
One Kanthal customer with extensive experience of utilizing Fibrothal® both for lithium-ion processes and elsewhere is OneJoon, a German-Korean mechanical engineering company and thermal processing equipment manufacturer.
“We use the Fibrothal® because it works!” exclaims Peter Vervoort, Vice President Process Development and Technology at OneJoon. “We wouldn’t want to change to anything else.”
OneJoon and Kanthal have worked together for more than five decades and, in the almost 45 years since the launch of Fibrothal®, there has been ample opportunity to put it to the test across a range of industries.
Fibrothal® is a “game changer”
“The oldest application where we still use Fibrothal® is in the razor blade industry, but we also use it for carbon fiber production and, of course, in the battery industry,” says Vervoort, who believes Fibrothal® is going to be a “game changer” for the battery business in the coming years.
“In the rapidly developing battery business, upscaling is the largest challenge we face,” he says. “Fibrothal® elements have helped us a great deal to achieve the temperature accuracy we need in order to scale up to large-scale furnaces.”
Meanwhile, Markus Mann has no doubt that the future of Fibrothal® is bright.
“We are moving toward the electrification of large-scale processes, and this is just the beginning,” he says. “Even though Fibrothal® is quite an old product, I believe we have only seen the start of what it’s capable of.”
Good can always be better!
Efficient and sustainable heating processes are vital when the lithium-ion battery industry scales up production to meet the fast-growing demand. Kanthal’s electric heating technology increases energy efficiency and productivity, while reducing emissions of CO2 and NOx. Learn more about the benefits for your process needs.