The galvanizing process provides protection with good adhesion that is durable over time, thus increasing the service life of the steel. To be done efficiently, it is important that the galvanizing furnace applies heat consistently as well as evenly over the entire width of the steel strip.
Galvanizing process in short
The galvanizing process involves applying a protective zinc coating to the steel. This is achieved by immersing the steel into molten zinc and kept at a temperature of around 460°C (860°F) so that it metallurgically bonds to the steel’s surface and forms an iron zinc alloy. When the steel returns to a normal atmosphere, a protective layer is formed which will help prevent corrosion and rust.
“If the temperature is not even, then the thickness of the coating and the properties of the steel will also differ,” says Susanne Selin, Senior R&D Project Manager, Kanthal. “You really want to be able to control the temperature in the furnace’s different zones, and also be able to adapt it quickly as you change the steel product going through.”
Electric heating’s advantages over gas
Susanne Selin, Senior R&D Project Manager, Kanthal.The most common heating solution used in galvanizing furnaces is gas heaters. However, an increasingly viable alternative is electric.The biggest advantage of electric heating is its superior temperature control, which allows operators to reach exact temperatures across the furnace’s different zones. In addition, thermal efficiency is much higher since no heat is lost through the exhaust gases.
“By replacing gas heaters with electric, you can remove all the pollution and fumes as well as significantly reduce the noise level,” Selin says. “It also improves workplace safety and reduces a lot of the maintenance work, since it removes the risk of gas leaks or other potential safety issues relating to the use of gas.”
A trouble-free solution
Based on its many years of experience with industrial electric heating, Kanthal’s optimal solution for galvanizing furnaces is its Tubothal® heating elementscombined with radiant tubes in Kanthal® APM or Kanthal® APMT iron-chromium-aluminum (FeCrAl) alloys.
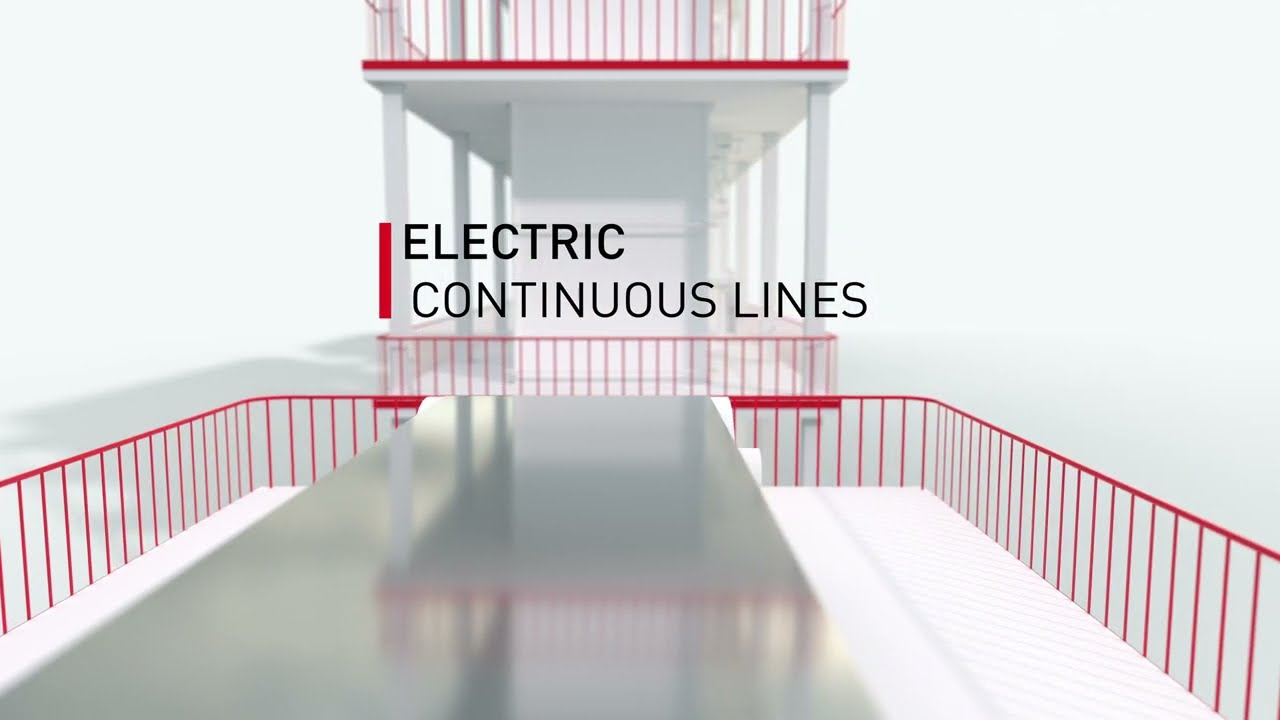
When you factor in the savings for maintenance as well as the lower energy consumption, this becomes a very cost-effective solution.
“Both of these alloys perform really well in all kinds of different atmospheres, in terms of oxidation and corrosion resistance,” Selin says. “Far less cleaning and maintenance is required compared with traditional heating elements. When you factor in the savings for maintenance as well as the lower energy consumption, this becomes a very cost-effective solution.”
Six benefits to using electric heating in galvanizing furnaces
- Increased thermal efficiency: Compared with gas heaters, far more of the heat generated by an electric heater is used in the furnace rather than lost with the exhaust gases.
- Precise temperature control: Compared with gas, an electric heater can be controlled to deliver exact temperatures.
- Excellent temperature uniformity: Electric heating delivers a consistent and even temperature across the whole steel strip.
- A cleaner, quieter and safer working environment: Electric heaters do not emit any harmful exhaust gases in the factory, while the noise levels are far lower.
- Zero CO2 emissions: If the electric heater is powered by renewable energy, then the process effectively becomes emissions-free.
- Minimal maintenance: With less oxidation, less maintenance and cleaning from combustion byproducts or spallation from the elements is required.
Read more
Electrification made easy